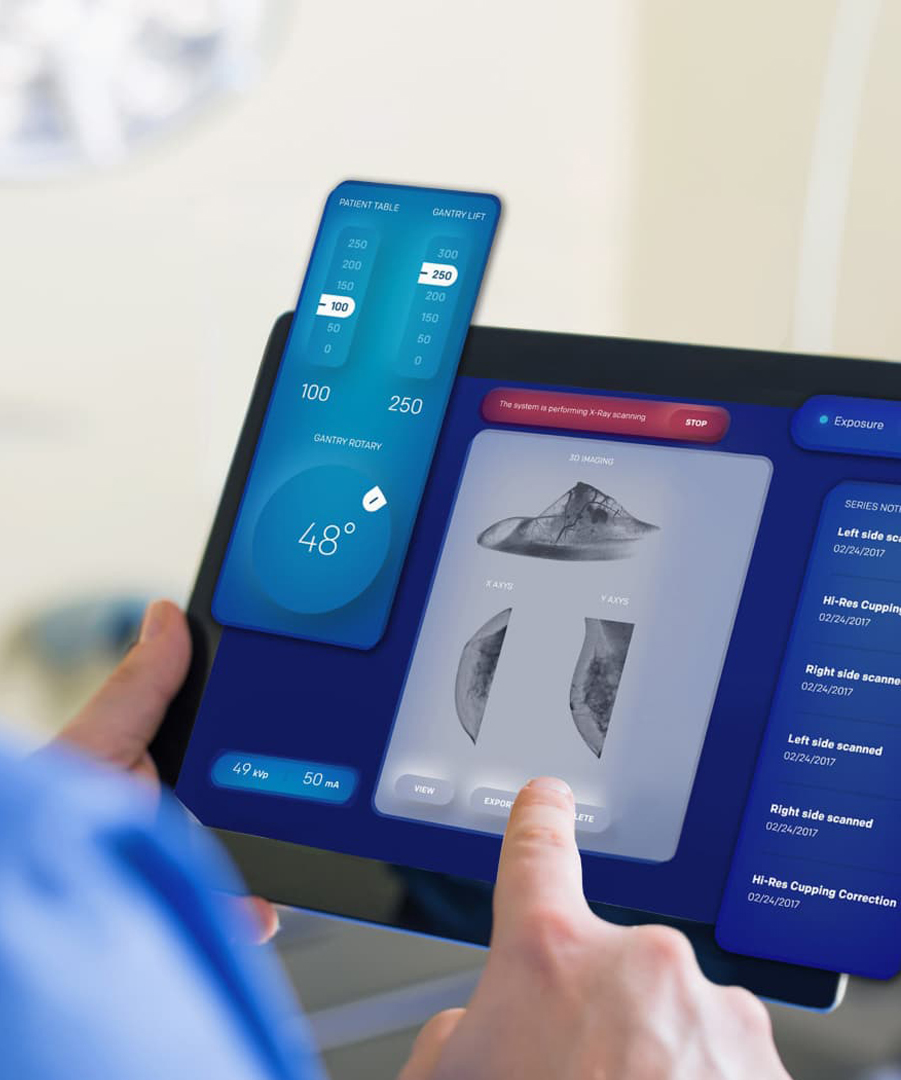
Designing and ordering fire apparatus involves complex technical specifications, regulatory compliance, and stakeholder coordination. Simplifying this process enhances efficiency and reduces delays. Standardizing core components—such as chassis, pump systems, or cabin layouts—enables modular customization. Departments can select pre-engineered modules that meet their operational needs (e.g., water tank capacity, ladder configurations) without reinventing the entire apparatus.
Consolidated vendors can manage component sourcing, assembly, and delivery timelines, reducing administrative burdens. Strategic partnerships also enable predictive inventory management, leveraging data analytics to anticipate part shortages or lead time fluctuations.
Below are three actionable strategies to achieve this:
Adopt Modular Design Frameworks
Transitioning from fully custom builds to modular designs accelerates production and minimizes errors. By pre-engineering standardized components (e.g., pump systems, chassis, or ladder mechanisms), fire trucks manufacturers can offer flexible configurations that meet diverse operational needs without reinventing core elements.
Implement Digital Collaboration Platforms
Replacing fragmented communication with integrated digital tools bridges gaps between fire departments, dealers, and manufacturers. Cloud-based platforms enable real-time collaboration on 3D models, material lists, and cost estimates, ensuring all stakeholders access up-to-date project data.
Leverage Pre-Configured Packages
Offering pre-configured apparatus packages for common scenarios (e.g., urban firefighting, hazmat response) simplifies decision-making. Departments can choose from tested, budget-aligned designs with predefined specifications, avoiding the overwhelm of custom options. fire trucks Dealers can further streamline procurement by bundling training, warranties, and financing into transparent packages.
You may be interested in the following information