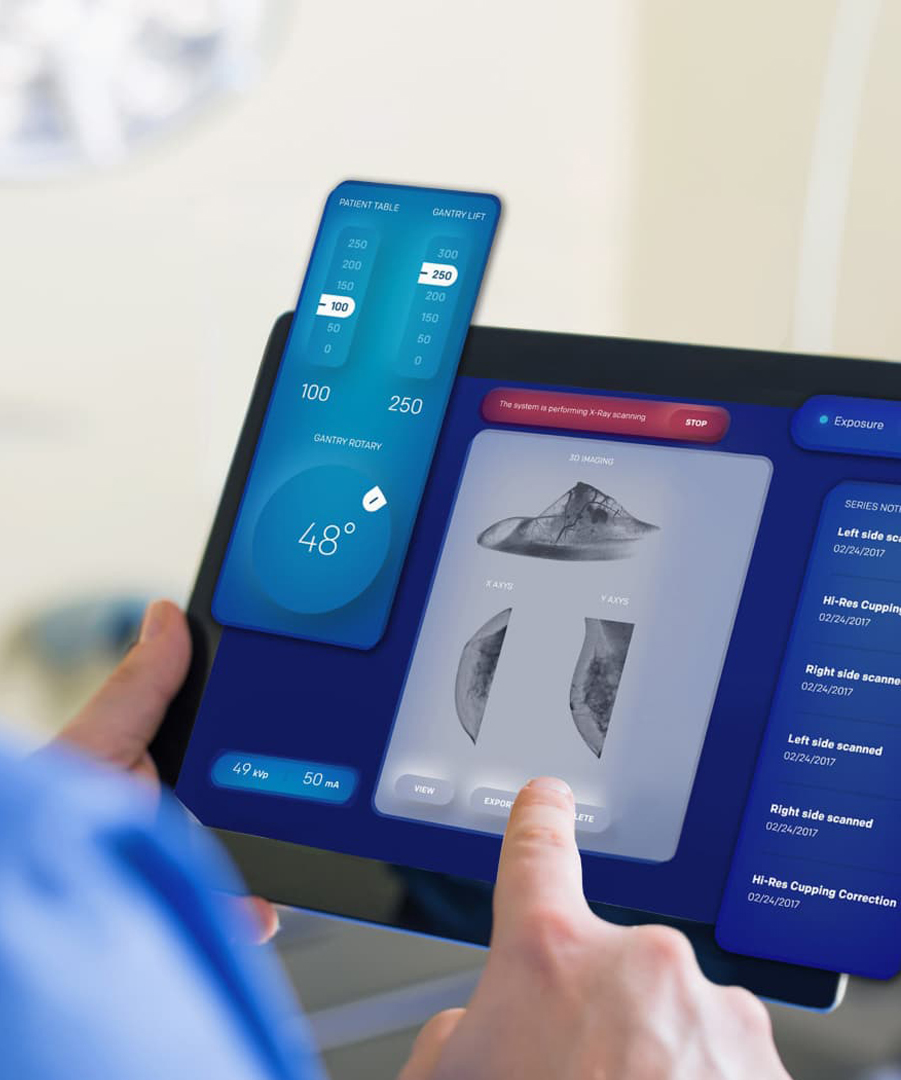
Acquiring firefighting equipment represents a dynamic yet intricate undertaking that shapes community safety infrastructure for decades. Strategizing apparatus procurement requires emergency service organizations to reconcile multifaceted operational parameters including response frequency, terrain characteristics, fiscal limitations, maintenance lifecycles, and evolving demographic demands. This critical decision-making process often becomes particularly daunting when constrained by compressed timelines and resource allocations.
To optimize equipment acquisition while maintaining operational simplicity, prioritize these three strategic pillars:
Fire-truck-needs-assessment
Initiating structured operational evaluations forms the cornerstone of efficient procurement workflows. Municipal fire service administrators should cross-reference established response protocols with evolving community risk profiles to determine equipment specifications. Key analytical dimensions encompass:
• Timeline and financial parameters
• Fleet composition and functional diversification
• Core operational responsibilities
• Secondary mission capabilities
• Geographical and regulatory compliance factors
• Apparatus maneuverability limitations
• Service demand projections
• Specialized equipment storage requirements
For enhanced planning support, consult specialized equipment configuration guides that detail component integration from fundamental elements to advanced modular systems. Industry consortium participation frequently enables optimized procurement through collective bidding advantages.
Fire-truck-dealer
Cultivating strategic alliances with certified equipment specialists ensures technical compliance while preserving customization requirements. Experienced distributors leverage regional deployment insights to recommend field-tested configurations, potentially reducing unnecessary modifications. Through synchronized production scheduling and iterative design reviews, manufacturers can align fabrication processes with municipal operational calendars, maintaining delivery commitments without compromising performance specifications.
Technical clarification resources like equipment terminology databases provide essential reference support throughout specification development phases.
Modern manufacturers now provide web-enabled visualization platforms that revolutionize equipment personalization workflows. Pierce Manufacturing's Build My Pierce™ (BMP™) system exemplifies this technological evolution, offering accelerated specification processes for customized apparatus while maintaining production efficiency. The platform enables:
• Modular cab configurations (Enforcer™, Saber®, Velocity®, Impel®)
• Specialized aerial systems (Ascendant® series platforms)
• Commercial tanker adaptations
• Multi-purpose pumper units
BMP™ enhances procurement efficiency through:
• Integrated design-to-delivery workflows
• Early specification finalization protocols
• 1,500+ validated customization parameters
• Market-proven technical configurations
• Engineered subsystem optimizations (suspension, safety features, power systems)
You may be interested in the following information