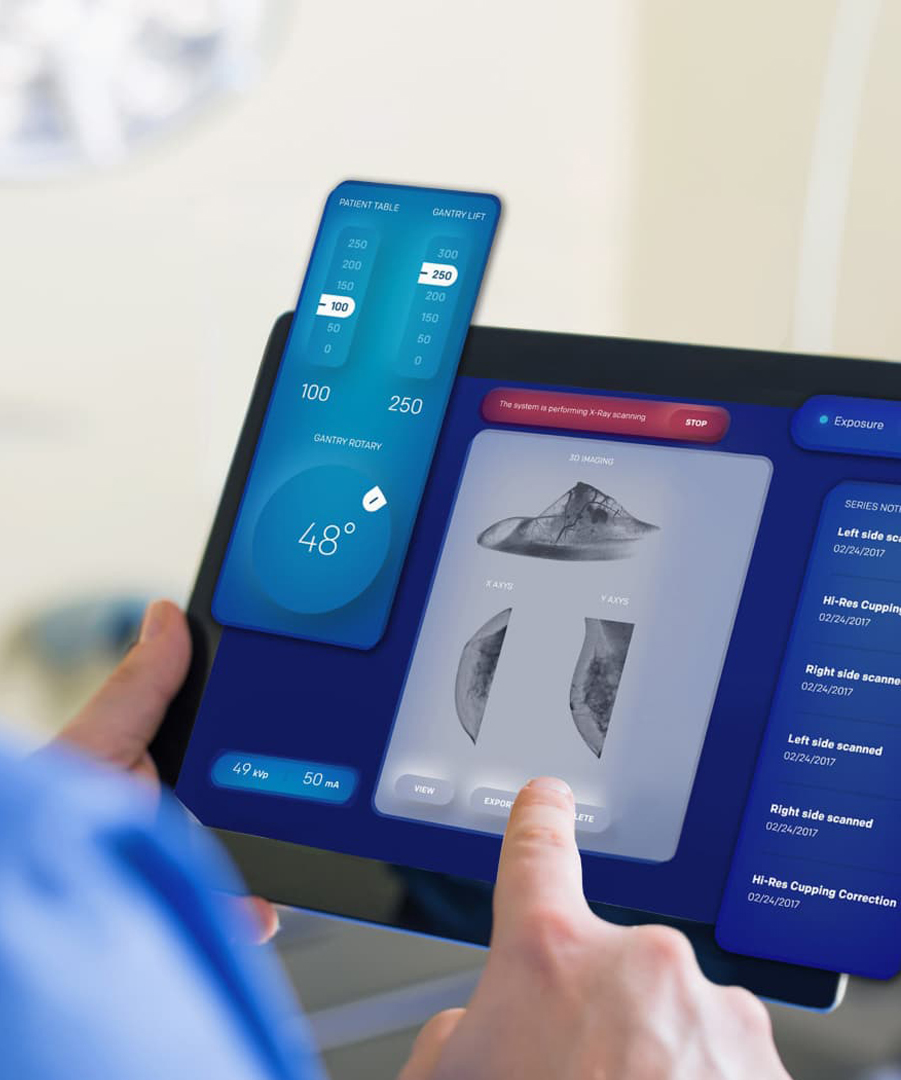
Crafting fire engines demands meticulous planning and a methodical sequence, requiring accuracy, creativity, and specialized knowledge. From initial metal cutting to final delivery, structured protocols ensure each custom unit surpasses client demands while delivering unmatched performance.
Powerstar Manufacturing’s dedicated team designs and assembles bespoke fire apparatus across 1.5+ million square feet of specialized facilities. Skilled professionals oversee every phase—welding to integration—mastering intricate details of pumpers, tankers, aerials, and heavy-rescue units. Continuous R&D investments keep Pierce at technology’s cutting edge, supported by dealer networks offering tailored consultations to meet exact client specifications.
Explore the intricate fire engine creation journey below, highlighting dedication infused into every component. Watch our video for a visual breakdown of the manufacturing workflow.
Metal Crafting for Fire Engines
A welder fabricates a fire engine cab during metal processing.
Initial stages involve shaping sheet metal via lasers, turret punches, and waterjets into cab panels, structural frames, doors, and subassemblies. Formed parts then undergo precision bending using press brakes and automated panel systems. Post-fabrication, welding transforms these elements into cohesive structures.
For departments planning new apparatus, our guide Fire Engine Design: Sequential Planning offers foundational insights.
Welding Stages
Robotic arms weld fire truck components.
Specialized teams handle distinct welding tasks—cab construction, bodywork, pump frameworks—all executed by Pierce-certified welders. Onsite CWIs validate craftsmanship, ensuring flawless assembly for every order.
Coating and Painting
A technician applies red paint in a controlled booth.
Post-welding, components receive protective e-coating or galvanization for corrosion resistance. Parallel painting involves:
This critical water-flow hub blends welding, plumbing, and electrical work. Each pump house adapts to department-specific valve configurations and control layouts, ensuring operational efficiency during emergencies. Progressive quality checks guarantee leak-free durability.
Chassis and Cab Integration
Workers install a fire truck’s chassis components.
Frame rails, axles, engines, and transmissions merge during chassis assembly. Cab construction progresses outward-in, incorporating dashboards, wiring, insulation, and seating. Rigorous inspections accompany each phase.
Technological Advancements
Facility upgrades incorporate AI-driven robotics and automated systems, enhancing productivity while maintaining safety standards. These investments reflect Pierce’s dedication to innovation and excellence.
Quality Assurance
A finished fire truck undergoes light-tunnel testing.
Final checks include:
Departments conduct final inspections, testing all features before accepting delivery. Pierce’s VIP Certification ensures full adherence to global safety benchmarks.
Explore custom fire engine ordering by contacting local dealers. Questions? Engage with our experts below!
You may be interested in the following information